3D Panel Production Line
3D Panel Production Line Flow Chart
- Assembling 3D Panel Machine
- Steel Wire Mesh Welding Machine
- Mesh Trolley
- Steel Wire Rack
- Air Compressor
- Compressed-Air Storage Tank
- Steel Wire
- Steel Wire
- Wire Straightening Machine
- Wire Coiling Machine
- Wire Mesh
- EPS Panels
- 3D Panels
3D Panel Production Line Process Flow
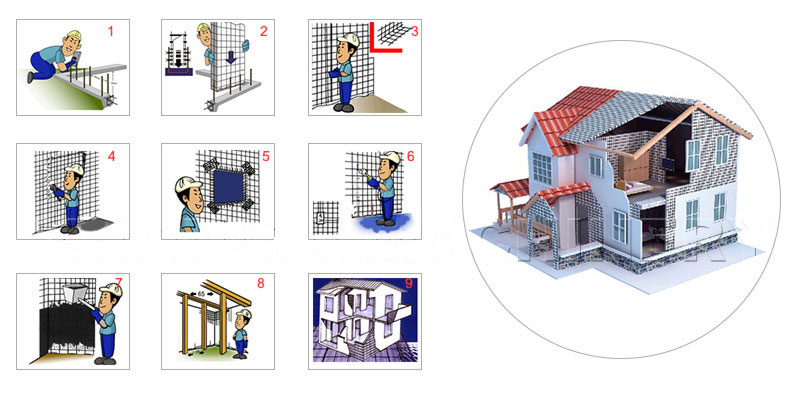
3D Panel Usage
-
) What is 3D panel?
3D panel is a prefabricated Three Dimensional Lightweight Structural panel consisting of a super-insulated polystyrene core sandwiched between two engineered layers of 10 ga Steel welded wire fabric mesh. To complete the panel form process a 10 ga Steel wire truss is pierced completely through the polystyrene core and welded to each of the outer layer sheets of 10 ga Steel welded wire fabric mesh. Once a special shotcrete concrete is applied to each side of the panel, the strong Three Dee insulated concrete structure is completed. The 3D Panel is a unique and effective way to easily create a strong insulated concrete building or wall. -
) 3D panel structure
Components of the 3D panel include :
- Foam core for insulation.
- Wire mesh on inside and outside.
- Welded truss of wire cross pieces.
- Sprayed concrete on both sides ("shotcrete").
-
) 3D panel raw material
- Low carbon steel wire (Normally 2.0mm -3.0mm)
- EPS(Expanded polystyrene) core (Normally 50-100mm)
-
) Normal 3D panel specifications:
Truss Wire:2.0mm -2.8mm galvanzied.
Mesh Wire:2-2.8mm Mesh hole:50 *52mm
Panel Length:3000mm or 6000mm
Panel width :1220mm EPS Insulation Core:50-100mm -
) 3D panel Properties
- Thermal Insulation: The EPS squeezing foaming polystyrene that is famous for the internal thermal insulation is used and reduces the loss of heat. It also makes the comfortable indoor space regardless of temperature variation in the winter season.
- Fireproofing: It has passed the 120 minutes fireproofing test of national construction institute and has also been approved as the fireproofing materials for internal & external construction stuffs.
- Moisture proofing: As we have used the high performance foaming polystyrene, it shows an excellent prevention against the condensation on the wall. (As for the usage of external wall, the exterior on the external wall needs the waterproofing mortar)
- Soundproofing :On the base of sound insulation performance test, it has shown a distinguished feature of soundproofing among others. Especially, it shows a heightened operation capability with both sides plasterboard.
- Lightweight: It only weighs a quarter of the masonry wall, which alleviates the fixed load of structure and also highly recommended in the enlargement of old buildings.
- Structure: It is used for every construction like residence and apartment and is highly recommended .
- Variety: It can be designed in a varied form without any professional knowledge, and fits for the round-typed materials as increasing 10% indoor space compared with masonry structure.
- Economical Efficiency: As it is a standardized factory product, easy to construct, and allows us to execute the masonry, insulation, plastering at the same time, it surely reduces the construction time down to a third.
- Shortening of Construction Time: As we said above, it is easy to execute and able to curtail the construction expense with the high efficiency in thermal insulation. It also boils down the framing expense as a lightweight material, which is definitely economically effective.
- Withstand earthquakes, hurricanes and typhoons: The monolithic structure with 3D panel enables it to withstand earthquakes, hurricanes and typhoons. Many 3D buildings have endured hurricanes with no water penetration or damage, earthquakes with no cracking, and at the same time provided a comfortable and energy-efficient environment for the residents.